How to fix a bad KF flange?
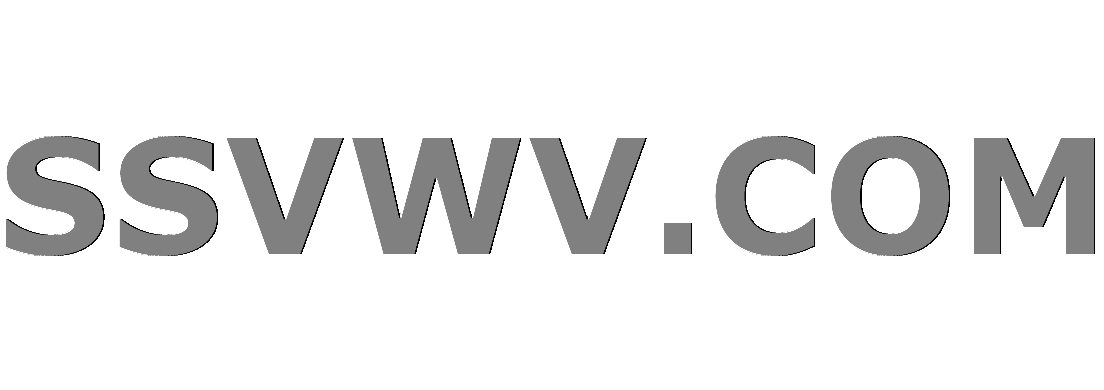
Multi tool use
$begingroup$
Here is an interesting question for those who are familiar with vacuum science techniques. In the attached picture we have a damaged surface of a KF flange, which comes from the turbo pump outlet and connects to a roughing pump. We believe this is a source of major leak (our roughing pump or helium leak-checker can pump out a small 4-way cross efficiently, but the same 4-way cross attached to the turbo pump (inlet sealed) cannot be pumped down efficiently).
How would one fix a scratched flange surface like this? Tried putting some silicone vacuum grease but didn't fix the problem.
experimental-physics experimental-technique
$endgroup$
add a comment |
$begingroup$
Here is an interesting question for those who are familiar with vacuum science techniques. In the attached picture we have a damaged surface of a KF flange, which comes from the turbo pump outlet and connects to a roughing pump. We believe this is a source of major leak (our roughing pump or helium leak-checker can pump out a small 4-way cross efficiently, but the same 4-way cross attached to the turbo pump (inlet sealed) cannot be pumped down efficiently).
How would one fix a scratched flange surface like this? Tried putting some silicone vacuum grease but didn't fix the problem.
experimental-physics experimental-technique
$endgroup$
add a comment |
$begingroup$
Here is an interesting question for those who are familiar with vacuum science techniques. In the attached picture we have a damaged surface of a KF flange, which comes from the turbo pump outlet and connects to a roughing pump. We believe this is a source of major leak (our roughing pump or helium leak-checker can pump out a small 4-way cross efficiently, but the same 4-way cross attached to the turbo pump (inlet sealed) cannot be pumped down efficiently).
How would one fix a scratched flange surface like this? Tried putting some silicone vacuum grease but didn't fix the problem.
experimental-physics experimental-technique
$endgroup$
Here is an interesting question for those who are familiar with vacuum science techniques. In the attached picture we have a damaged surface of a KF flange, which comes from the turbo pump outlet and connects to a roughing pump. We believe this is a source of major leak (our roughing pump or helium leak-checker can pump out a small 4-way cross efficiently, but the same 4-way cross attached to the turbo pump (inlet sealed) cannot be pumped down efficiently).
How would one fix a scratched flange surface like this? Tried putting some silicone vacuum grease but didn't fix the problem.
experimental-physics experimental-technique
experimental-physics experimental-technique
edited 18 mins ago


Chair
3,68472034
3,68472034
asked 1 hour ago


IamAStudentIamAStudent
754112
754112
add a comment |
add a comment |
2 Answers
2
active
oldest
votes
$begingroup$
I have fixed flanges like this by sanding. If your flange is aluminum, this won't be too hard; if it's stainless, it might be fairly tedious and painful!
Start with a coarse-grit sandpaper, around P120-P200, and sand out the visible dents and scratches. Then work your way through a couple of intermediate grits up to at least P600. Sand in a circular motion around the flange to avoid making scratches that cross the o-ring. Make sure to moisten the sandpaper (I usually use isopropanol) to keep the dust down and to plug the exhaust tube and clean its outlet regularly while you work, as you don't want any of the grit to migrate into your turbo.
As a side note, I've found Apiezon L to be a very good low-outgassing grease for ultra-high vacuum, but it's always better to fix leaks if you can rather than greasing and hoping for the best.
New contributor
fiddlehead is a new contributor to this site. Take care in asking for clarification, commenting, and answering.
Check out our Code of Conduct.
$endgroup$
$begingroup$
The flange is indeed stainless steel, as it is part of a turbo pump. How do you make sure your surface is flat as you sand away the rough surface?
$endgroup$
– IamAStudent
1 hour ago
$begingroup$
I would use a flat piece of metal stock (like a small block of aluminum) to hold the sandpaper flush with the flange surface. I wouldn't worry too much about it being perfectly flat, as your rubber o-ring can flex to accommodate large-scale surface unevenness.
$endgroup$
– fiddlehead
1 hour ago
add a comment |
$begingroup$
I can think of three possible fixes:
1) The easiest "work-around" involves using a teflon gasket. Teflon is known to cold flow and conform to the shape that it is clamped between. With sufficient compression, such a gasket should fill in the gaps that obviously exist in your present flange face. Assuming that this works, you will probably want to keep quite a few teflon gaskets on hand, as each time you compress the gasket, the teflon would get squeezed to thinner and thinner dimensions.
2) Have a good machinist resurface the current flange face.
3) Cut off the existing flange and weld a new one on. This is probably not an option, or you would have done it already.
$endgroup$
$begingroup$
Dear David, your proposal 1) sounds interesting. I tried vendors such as Kurt J Lesker or Duniway stockroom but couldn't find teflon gaskets for the type of flange I am using. Could you recommend where I may find such compatible teflon gaskets?
$endgroup$
– IamAStudent
1 hour ago
add a comment |
Your Answer
StackExchange.ifUsing("editor", function () {
return StackExchange.using("mathjaxEditing", function () {
StackExchange.MarkdownEditor.creationCallbacks.add(function (editor, postfix) {
StackExchange.mathjaxEditing.prepareWmdForMathJax(editor, postfix, [["$", "$"], ["\\(","\\)"]]);
});
});
}, "mathjax-editing");
StackExchange.ready(function() {
var channelOptions = {
tags: "".split(" "),
id: "151"
};
initTagRenderer("".split(" "), "".split(" "), channelOptions);
StackExchange.using("externalEditor", function() {
// Have to fire editor after snippets, if snippets enabled
if (StackExchange.settings.snippets.snippetsEnabled) {
StackExchange.using("snippets", function() {
createEditor();
});
}
else {
createEditor();
}
});
function createEditor() {
StackExchange.prepareEditor({
heartbeatType: 'answer',
autoActivateHeartbeat: false,
convertImagesToLinks: false,
noModals: true,
showLowRepImageUploadWarning: true,
reputationToPostImages: null,
bindNavPrevention: true,
postfix: "",
imageUploader: {
brandingHtml: "Powered by u003ca class="icon-imgur-white" href="https://imgur.com/"u003eu003c/au003e",
contentPolicyHtml: "User contributions licensed under u003ca href="https://creativecommons.org/licenses/by-sa/3.0/"u003ecc by-sa 3.0 with attribution requiredu003c/au003e u003ca href="https://stackoverflow.com/legal/content-policy"u003e(content policy)u003c/au003e",
allowUrls: true
},
noCode: true, onDemand: true,
discardSelector: ".discard-answer"
,immediatelyShowMarkdownHelp:true
});
}
});
Sign up or log in
StackExchange.ready(function () {
StackExchange.helpers.onClickDraftSave('#login-link');
});
Sign up using Google
Sign up using Facebook
Sign up using Email and Password
Post as a guest
Required, but never shown
StackExchange.ready(
function () {
StackExchange.openid.initPostLogin('.new-post-login', 'https%3a%2f%2fphysics.stackexchange.com%2fquestions%2f456512%2fhow-to-fix-a-bad-kf-flange%23new-answer', 'question_page');
}
);
Post as a guest
Required, but never shown
2 Answers
2
active
oldest
votes
2 Answers
2
active
oldest
votes
active
oldest
votes
active
oldest
votes
$begingroup$
I have fixed flanges like this by sanding. If your flange is aluminum, this won't be too hard; if it's stainless, it might be fairly tedious and painful!
Start with a coarse-grit sandpaper, around P120-P200, and sand out the visible dents and scratches. Then work your way through a couple of intermediate grits up to at least P600. Sand in a circular motion around the flange to avoid making scratches that cross the o-ring. Make sure to moisten the sandpaper (I usually use isopropanol) to keep the dust down and to plug the exhaust tube and clean its outlet regularly while you work, as you don't want any of the grit to migrate into your turbo.
As a side note, I've found Apiezon L to be a very good low-outgassing grease for ultra-high vacuum, but it's always better to fix leaks if you can rather than greasing and hoping for the best.
New contributor
fiddlehead is a new contributor to this site. Take care in asking for clarification, commenting, and answering.
Check out our Code of Conduct.
$endgroup$
$begingroup$
The flange is indeed stainless steel, as it is part of a turbo pump. How do you make sure your surface is flat as you sand away the rough surface?
$endgroup$
– IamAStudent
1 hour ago
$begingroup$
I would use a flat piece of metal stock (like a small block of aluminum) to hold the sandpaper flush with the flange surface. I wouldn't worry too much about it being perfectly flat, as your rubber o-ring can flex to accommodate large-scale surface unevenness.
$endgroup$
– fiddlehead
1 hour ago
add a comment |
$begingroup$
I have fixed flanges like this by sanding. If your flange is aluminum, this won't be too hard; if it's stainless, it might be fairly tedious and painful!
Start with a coarse-grit sandpaper, around P120-P200, and sand out the visible dents and scratches. Then work your way through a couple of intermediate grits up to at least P600. Sand in a circular motion around the flange to avoid making scratches that cross the o-ring. Make sure to moisten the sandpaper (I usually use isopropanol) to keep the dust down and to plug the exhaust tube and clean its outlet regularly while you work, as you don't want any of the grit to migrate into your turbo.
As a side note, I've found Apiezon L to be a very good low-outgassing grease for ultra-high vacuum, but it's always better to fix leaks if you can rather than greasing and hoping for the best.
New contributor
fiddlehead is a new contributor to this site. Take care in asking for clarification, commenting, and answering.
Check out our Code of Conduct.
$endgroup$
$begingroup$
The flange is indeed stainless steel, as it is part of a turbo pump. How do you make sure your surface is flat as you sand away the rough surface?
$endgroup$
– IamAStudent
1 hour ago
$begingroup$
I would use a flat piece of metal stock (like a small block of aluminum) to hold the sandpaper flush with the flange surface. I wouldn't worry too much about it being perfectly flat, as your rubber o-ring can flex to accommodate large-scale surface unevenness.
$endgroup$
– fiddlehead
1 hour ago
add a comment |
$begingroup$
I have fixed flanges like this by sanding. If your flange is aluminum, this won't be too hard; if it's stainless, it might be fairly tedious and painful!
Start with a coarse-grit sandpaper, around P120-P200, and sand out the visible dents and scratches. Then work your way through a couple of intermediate grits up to at least P600. Sand in a circular motion around the flange to avoid making scratches that cross the o-ring. Make sure to moisten the sandpaper (I usually use isopropanol) to keep the dust down and to plug the exhaust tube and clean its outlet regularly while you work, as you don't want any of the grit to migrate into your turbo.
As a side note, I've found Apiezon L to be a very good low-outgassing grease for ultra-high vacuum, but it's always better to fix leaks if you can rather than greasing and hoping for the best.
New contributor
fiddlehead is a new contributor to this site. Take care in asking for clarification, commenting, and answering.
Check out our Code of Conduct.
$endgroup$
I have fixed flanges like this by sanding. If your flange is aluminum, this won't be too hard; if it's stainless, it might be fairly tedious and painful!
Start with a coarse-grit sandpaper, around P120-P200, and sand out the visible dents and scratches. Then work your way through a couple of intermediate grits up to at least P600. Sand in a circular motion around the flange to avoid making scratches that cross the o-ring. Make sure to moisten the sandpaper (I usually use isopropanol) to keep the dust down and to plug the exhaust tube and clean its outlet regularly while you work, as you don't want any of the grit to migrate into your turbo.
As a side note, I've found Apiezon L to be a very good low-outgassing grease for ultra-high vacuum, but it's always better to fix leaks if you can rather than greasing and hoping for the best.
New contributor
fiddlehead is a new contributor to this site. Take care in asking for clarification, commenting, and answering.
Check out our Code of Conduct.
New contributor
fiddlehead is a new contributor to this site. Take care in asking for clarification, commenting, and answering.
Check out our Code of Conduct.
answered 1 hour ago
fiddleheadfiddlehead
512
512
New contributor
fiddlehead is a new contributor to this site. Take care in asking for clarification, commenting, and answering.
Check out our Code of Conduct.
New contributor
fiddlehead is a new contributor to this site. Take care in asking for clarification, commenting, and answering.
Check out our Code of Conduct.
fiddlehead is a new contributor to this site. Take care in asking for clarification, commenting, and answering.
Check out our Code of Conduct.
$begingroup$
The flange is indeed stainless steel, as it is part of a turbo pump. How do you make sure your surface is flat as you sand away the rough surface?
$endgroup$
– IamAStudent
1 hour ago
$begingroup$
I would use a flat piece of metal stock (like a small block of aluminum) to hold the sandpaper flush with the flange surface. I wouldn't worry too much about it being perfectly flat, as your rubber o-ring can flex to accommodate large-scale surface unevenness.
$endgroup$
– fiddlehead
1 hour ago
add a comment |
$begingroup$
The flange is indeed stainless steel, as it is part of a turbo pump. How do you make sure your surface is flat as you sand away the rough surface?
$endgroup$
– IamAStudent
1 hour ago
$begingroup$
I would use a flat piece of metal stock (like a small block of aluminum) to hold the sandpaper flush with the flange surface. I wouldn't worry too much about it being perfectly flat, as your rubber o-ring can flex to accommodate large-scale surface unevenness.
$endgroup$
– fiddlehead
1 hour ago
$begingroup$
The flange is indeed stainless steel, as it is part of a turbo pump. How do you make sure your surface is flat as you sand away the rough surface?
$endgroup$
– IamAStudent
1 hour ago
$begingroup$
The flange is indeed stainless steel, as it is part of a turbo pump. How do you make sure your surface is flat as you sand away the rough surface?
$endgroup$
– IamAStudent
1 hour ago
$begingroup$
I would use a flat piece of metal stock (like a small block of aluminum) to hold the sandpaper flush with the flange surface. I wouldn't worry too much about it being perfectly flat, as your rubber o-ring can flex to accommodate large-scale surface unevenness.
$endgroup$
– fiddlehead
1 hour ago
$begingroup$
I would use a flat piece of metal stock (like a small block of aluminum) to hold the sandpaper flush with the flange surface. I wouldn't worry too much about it being perfectly flat, as your rubber o-ring can flex to accommodate large-scale surface unevenness.
$endgroup$
– fiddlehead
1 hour ago
add a comment |
$begingroup$
I can think of three possible fixes:
1) The easiest "work-around" involves using a teflon gasket. Teflon is known to cold flow and conform to the shape that it is clamped between. With sufficient compression, such a gasket should fill in the gaps that obviously exist in your present flange face. Assuming that this works, you will probably want to keep quite a few teflon gaskets on hand, as each time you compress the gasket, the teflon would get squeezed to thinner and thinner dimensions.
2) Have a good machinist resurface the current flange face.
3) Cut off the existing flange and weld a new one on. This is probably not an option, or you would have done it already.
$endgroup$
$begingroup$
Dear David, your proposal 1) sounds interesting. I tried vendors such as Kurt J Lesker or Duniway stockroom but couldn't find teflon gaskets for the type of flange I am using. Could you recommend where I may find such compatible teflon gaskets?
$endgroup$
– IamAStudent
1 hour ago
add a comment |
$begingroup$
I can think of three possible fixes:
1) The easiest "work-around" involves using a teflon gasket. Teflon is known to cold flow and conform to the shape that it is clamped between. With sufficient compression, such a gasket should fill in the gaps that obviously exist in your present flange face. Assuming that this works, you will probably want to keep quite a few teflon gaskets on hand, as each time you compress the gasket, the teflon would get squeezed to thinner and thinner dimensions.
2) Have a good machinist resurface the current flange face.
3) Cut off the existing flange and weld a new one on. This is probably not an option, or you would have done it already.
$endgroup$
$begingroup$
Dear David, your proposal 1) sounds interesting. I tried vendors such as Kurt J Lesker or Duniway stockroom but couldn't find teflon gaskets for the type of flange I am using. Could you recommend where I may find such compatible teflon gaskets?
$endgroup$
– IamAStudent
1 hour ago
add a comment |
$begingroup$
I can think of three possible fixes:
1) The easiest "work-around" involves using a teflon gasket. Teflon is known to cold flow and conform to the shape that it is clamped between. With sufficient compression, such a gasket should fill in the gaps that obviously exist in your present flange face. Assuming that this works, you will probably want to keep quite a few teflon gaskets on hand, as each time you compress the gasket, the teflon would get squeezed to thinner and thinner dimensions.
2) Have a good machinist resurface the current flange face.
3) Cut off the existing flange and weld a new one on. This is probably not an option, or you would have done it already.
$endgroup$
I can think of three possible fixes:
1) The easiest "work-around" involves using a teflon gasket. Teflon is known to cold flow and conform to the shape that it is clamped between. With sufficient compression, such a gasket should fill in the gaps that obviously exist in your present flange face. Assuming that this works, you will probably want to keep quite a few teflon gaskets on hand, as each time you compress the gasket, the teflon would get squeezed to thinner and thinner dimensions.
2) Have a good machinist resurface the current flange face.
3) Cut off the existing flange and weld a new one on. This is probably not an option, or you would have done it already.
answered 1 hour ago
David WhiteDavid White
4,1531619
4,1531619
$begingroup$
Dear David, your proposal 1) sounds interesting. I tried vendors such as Kurt J Lesker or Duniway stockroom but couldn't find teflon gaskets for the type of flange I am using. Could you recommend where I may find such compatible teflon gaskets?
$endgroup$
– IamAStudent
1 hour ago
add a comment |
$begingroup$
Dear David, your proposal 1) sounds interesting. I tried vendors such as Kurt J Lesker or Duniway stockroom but couldn't find teflon gaskets for the type of flange I am using. Could you recommend where I may find such compatible teflon gaskets?
$endgroup$
– IamAStudent
1 hour ago
$begingroup$
Dear David, your proposal 1) sounds interesting. I tried vendors such as Kurt J Lesker or Duniway stockroom but couldn't find teflon gaskets for the type of flange I am using. Could you recommend where I may find such compatible teflon gaskets?
$endgroup$
– IamAStudent
1 hour ago
$begingroup$
Dear David, your proposal 1) sounds interesting. I tried vendors such as Kurt J Lesker or Duniway stockroom but couldn't find teflon gaskets for the type of flange I am using. Could you recommend where I may find such compatible teflon gaskets?
$endgroup$
– IamAStudent
1 hour ago
add a comment |
Thanks for contributing an answer to Physics Stack Exchange!
- Please be sure to answer the question. Provide details and share your research!
But avoid …
- Asking for help, clarification, or responding to other answers.
- Making statements based on opinion; back them up with references or personal experience.
Use MathJax to format equations. MathJax reference.
To learn more, see our tips on writing great answers.
Sign up or log in
StackExchange.ready(function () {
StackExchange.helpers.onClickDraftSave('#login-link');
});
Sign up using Google
Sign up using Facebook
Sign up using Email and Password
Post as a guest
Required, but never shown
StackExchange.ready(
function () {
StackExchange.openid.initPostLogin('.new-post-login', 'https%3a%2f%2fphysics.stackexchange.com%2fquestions%2f456512%2fhow-to-fix-a-bad-kf-flange%23new-answer', 'question_page');
}
);
Post as a guest
Required, but never shown
Sign up or log in
StackExchange.ready(function () {
StackExchange.helpers.onClickDraftSave('#login-link');
});
Sign up using Google
Sign up using Facebook
Sign up using Email and Password
Post as a guest
Required, but never shown
Sign up or log in
StackExchange.ready(function () {
StackExchange.helpers.onClickDraftSave('#login-link');
});
Sign up using Google
Sign up using Facebook
Sign up using Email and Password
Post as a guest
Required, but never shown
Sign up or log in
StackExchange.ready(function () {
StackExchange.helpers.onClickDraftSave('#login-link');
});
Sign up using Google
Sign up using Facebook
Sign up using Email and Password
Sign up using Google
Sign up using Facebook
Sign up using Email and Password
Post as a guest
Required, but never shown
Required, but never shown
Required, but never shown
Required, but never shown
Required, but never shown
Required, but never shown
Required, but never shown
Required, but never shown
Required, but never shown
0Tdi,3DDW,x6YErV6UIwRTIL2R9FuYws7BcJxLxd0 AF1dxpJ,2X